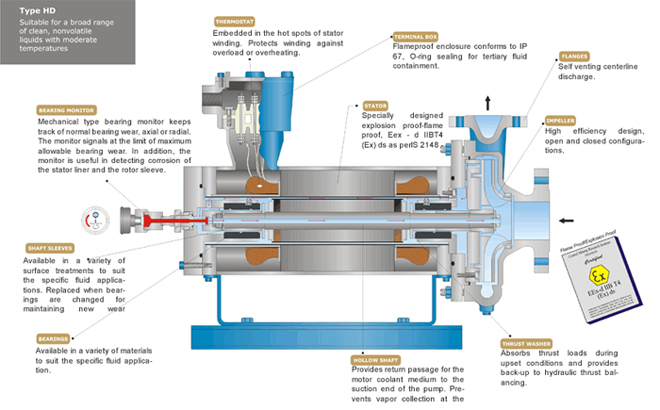
Pump Reliability
With the increasingly stringent demands on environmental protection, industries are seeking totally reliable ZERO EMISSION PUMPS.
Problems
Reliability of pimping operations is of supreme importance in handling critical services. In the case of conventional centrifugal pumps the integrity is always In questions. The mechanical seal has forever been the weak point of these pumps. The pumps are never 100% leak free and require regular maintenance and constant monitoring of the shaft seals, antifriction bearings and the flushing plan systems. The availability and the life of the ump is affected by the vulnerability of these components. It would be worthwhile to eliminate the weak spots in centrifugal pumps to achieve total reliability and leak free pumping.
Solution… Canned Motor Pumps
Canned Motor Pumps are indeed the logical solution for safe, zero emission pumping. The canned motor pump, originally designed to meet zero leakage and maximum reliability demands of the nuclear power stations, is now widely used in general industry. In particular, they excel in applications involving aggressive. Inflammable, explosive and toxic liquids because of the important advantages they offer over conventional centrifugal pumps. The construction of the Hydrodyne pump is hermetically sealed and provides primary and secondary fluid containment, the process fluid would never need to breach two separate physical barriers before any leakage from the pump/motor unit can occur. Also, as there is no external shaft in a canned motor pump, there is no need for any costly and troublesome on-site shaft alignment, unlike conventionally sealed or long-coupled mag-drive pumps where alignment between the pump shaft and motor seal is required. As the pump and motor are combined in a canned motor pump, the number of wearing parts is reduced, thereby reducing the stock of spare parts required.
Benefits
- No seals to replace
- Emissions free
- No product loss
- Flame proof/explosion proof
- No external lubrication
- No coupling
- No vibration
- No misalignment on thermal shock
- Negligible maintenance
- No rigid foundation
- Compact – saves 50% space
- Safe Operation